VIVO Joint Simulator
AMTI’s VIVO brings new life to joint motion simulation, dramatically increasing the kinetic and kinematic realism of simulation to provide the closest possible approach to in-vivo conditions. The VIVO provides the world’s first full-speed, full-load, six DOF environment in which to test joint prostheses and biological joint specimens. The VIVO’s workspace and compact packaging are designed to facilitate human joint studies while minimizing the use of laboratory floor space.
An accurate simulation of the kinematics, kinetics and durability of a joint’s structure requires accurate re-creation of the joint contact forces experienced in-vivo. Since soft-tissue forces can contribute very significantly to the joint contact force, a realistic simulation environment must include a way to simulate the effects of soft tissue forces. The VIVO supports two patented virtual soft tissue models: the exclusive multi-fiber ligament model and the heuristic constraint model for every axis of the VIVO that is in force-control mode.
VIVO's Key Performance Features:
Bringing new life to joint motion simulation
Accessories
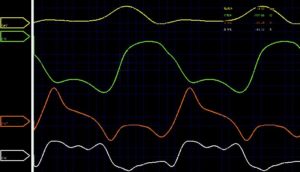
Vivo Control Software
(Included)
- User interface for controlling VIVO
- Supervisory functions
- Powerful motion programming tools
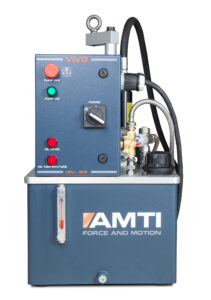
Hydraulic Power Unit
(Required)
- 5hp or 20hp HPU
- Gravity return
- 10′ supply & drain hose
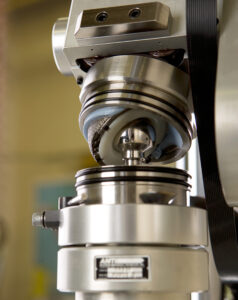
Hip Test Kit
(Optional)
- Optional fixture
- Hip implant/specimen testing
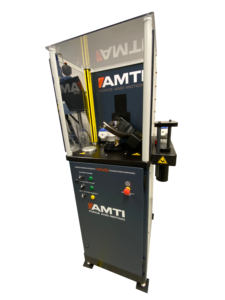
Load Soak Station
(Optional)
- Attaches to rightmost VIVO station
- Follows actuator pressure for Fz axis
Specifications & Details
Review detailed VIVO joint simulator specifications below.