Optima Technology
The best science begins with the best measurements.
Optima Calibration Technology
AMTI’s patented Optima calibration is a revolutionary development in force measurement technology, offering a 10-fold improvement over any force platform system on the market.
Using AMTI’s new optimized strain gage technology, the Optima-HPS force plate model provides levels of accuracy never before seen in force platform systems:
- Average COP accuracy of just a fraction of a millimeter (typically less than 0.2 mm)
- Crosstalk values typically ±0.05% of applied load
- Measurement accuracy typically ±0.1% of applied load*
How do we know the performance of the Optima-HPS is that good?
AMTI verifies the accuracy of each Optima system through a proprietary precision calibration that takes up to 4000 measurements throughout the platform’s entire rated capacity. This process uses a high-density calibration grid that covers the entire platform surface and uses fully documented NIST-traceable standards.
Each Optima HPS is composed of an Optima Force Plate, Optima Signal Conditioner, Optima Calibration Certificate, and cabling.
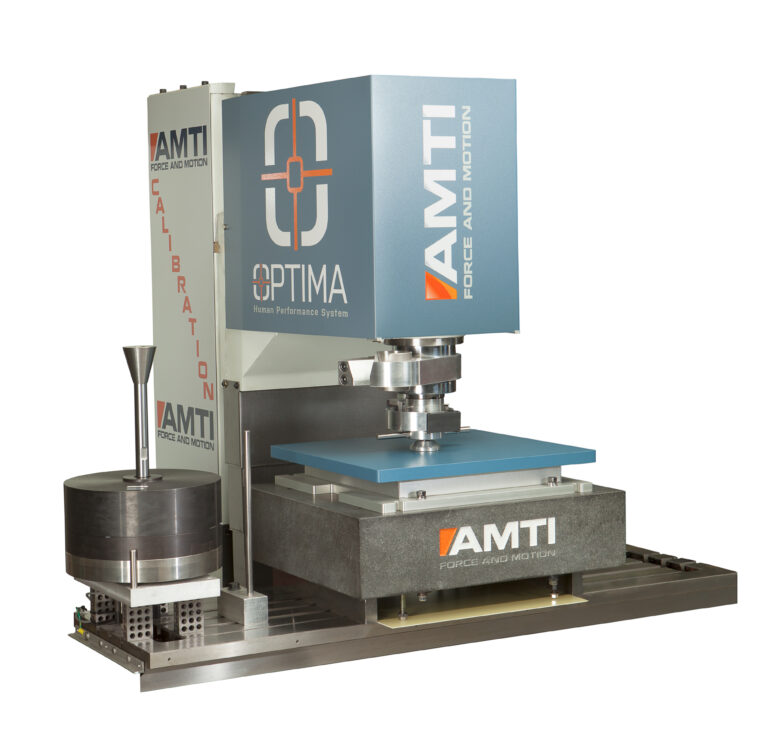
Precision Calibration Overview
The calibration of an Optima system is an exacting process involving up to 4000 measurements taken over the entire working surface. Multiple loads are applied at up to 400 locations using a precision machine capable of maintaining absolute positioning accuracy of 0.005 mm (certified by The Association For Manufacturing Technology).
This exhaustive calibration and verification process ensures that each Optima system offers the best possible quality, accuracy, and performance available.
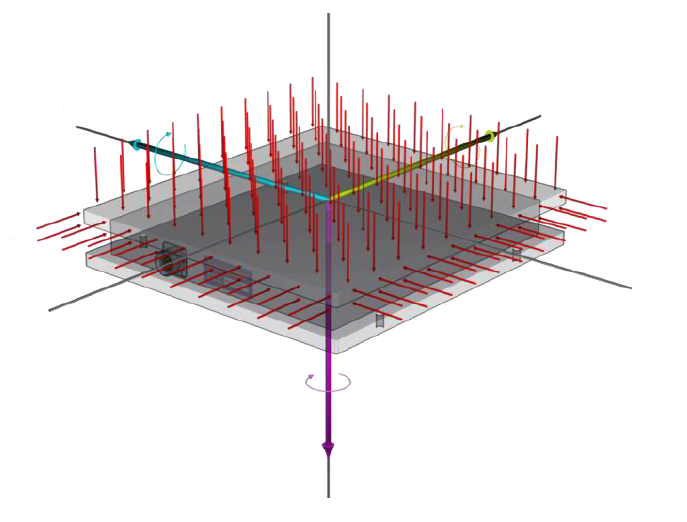
Optima Series Available
AMTI’s Optima technology is broken down into four series, each providing its own unique advantage.
- Optima-HPS (High Performance Series)
- Optima-BMS (Biomechanics Measurement Series)
- Optima-MMS (Medical Measurement Series)
- Optima-SPS (Special Purpose Series)
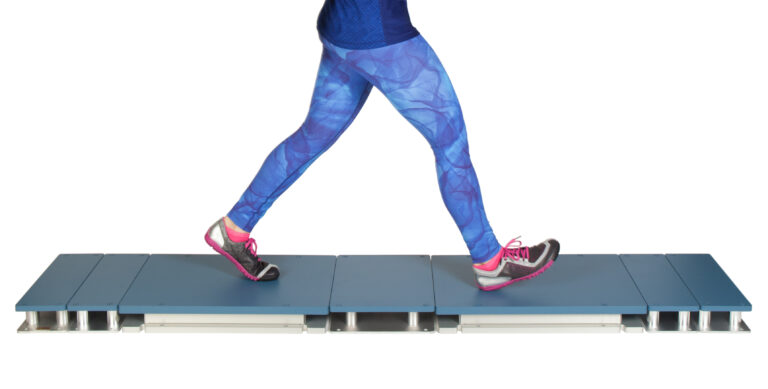
Contact AMTI to request a quote for the ‘gold standard’ Optima-HPS400600.
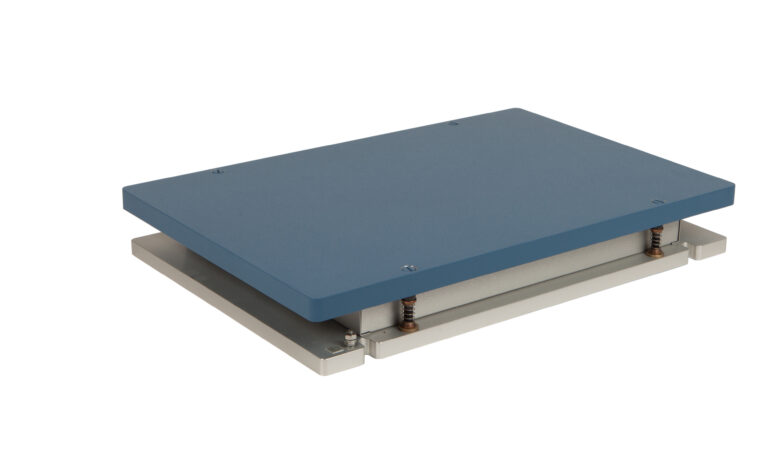